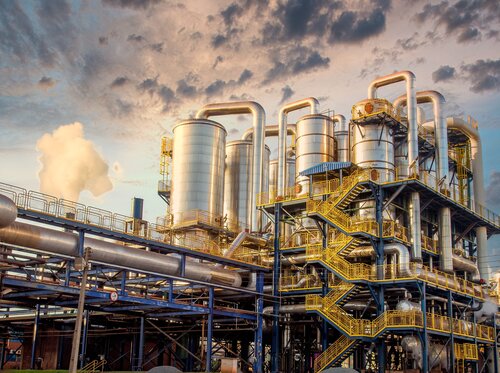
© istockphoto.com / Mailson Pignata
Process Plant Engineering
Chemical plants from FEED and process design through to detailed engineering
Contact:
The basis control concept created in the P&ID, for example, indicates the number of input/output channels required to the engineers. At the same time, the consumer lists provide the parameters for power distribution and its control. Here once again, standardized templates make it possible to plan complete control cabinets. Besides amalgamating all engineering results, Engineering Base also generates the entire plant documentation in accordance with the applicable IEC, ISA and ISO standards, complete with automatic change detection and version control.
The automation system's logic can be designed separately from the hardware in Engineering Base. This is where the control requirements of the P&IDs are implemented and further safety mechanisms are created. Any alarms and signals that are required can be specified directly in greater detail and can also continue to be refined and used in the subsequent workflows. The signal and alarm lists in Engineering Base are kept constantly updated and serve as the basis for both the software reports and the cause-and-effect matrices for the commissioning phase.
The hardware and software design process speeds up configuration and programming of the automation systems. Data is generated in neutral formats that allow it to be transferred to manufacturer-specific destination systems using widely used digital data exchange formats, such as Excel or AutomationML. This will ideally allow a completely predefined and tested module to be planned, built and implemented with minimal effort.