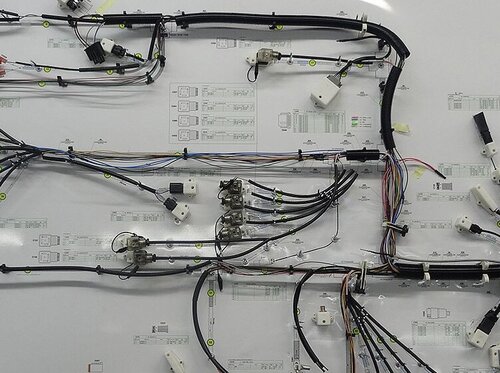
3D Wiring Harness Integration
From modular design to modular manufacturing
Contact:
The electrical components in a vehicle are connected by means of its electrical distribution system. Electrical and geometric properties must be taken into account during development, along with a multitude of possible variants. So there is a lot of potential for optimizing the overall development process through automation and virtualization.
Electrical components that communicate with one another are used to meet the requirements of an electrical system. A top-down approach is often used for development, which allows the system architecture to be specified gradually. Guaranteed data consistency, traceability and openness for both upstream and downstream processes are key requirements for modern engineering.
Before harnesses can be manufactured or cables installed in vehicles, the development data must be processed in order to provide special drawings or reports as well as data for production systems. Flexible data import and export capabilities coupled with automation allow this to be done with the requisite efficiency and data quality.
High-quality documentation for vehicle servicing and operation and as an aid for development, manufacturing and integration processes is essential. Preparation of this documentation can often be automated. The documentation generated can also be enhanced with helpful additional information and specific aspects can be visualized.
Cables and cable bundles in ships and trains are often laid in special cable trays. Many electrical and mechanical factors need to be taken into account when laying cables in these ducts. Optimizing routing and the processes involved opens up considerable potential for cost savings in both the planning and manufacturing phases.
Deep integration of software into an existing IT environment usually involves a great deal of effort. It's a different story with Engineering Base, however. The software is designed as an open system from the ground up, while also offering standard integration with numerous systems. And this integration capability can be easily expanded too.
Developers of electrical systems often work using a variety of systems as most tools are not flexible enough to effectively support the work carried out by different disciplines. Engineering Base is the exception here: the software can adapt to all manner of different requirements and combines graphical and alphanumeric data.
Almost every type of vehicle comes in a wide range of equipment variants. If individual configuration and documentation for each vehicle is required, modular design based on a construction kit is the best approach. In the automotive industry, however, harnesses should have a 150% design that models all possible combinations of modules or variants. Here again, we offer the ideal solution, by using relationships to map associations to modules or variants in the digital twin. Document-based tools cannot do this.
The Engineering Base data model allows information to be captured as soon as it is available without any requirements first having to be met. This data is then structured in such a way that it can be easily analyzed and processed by automated algorithms. This automates development processes and makes them more efficient.