Engineering for 3 metric tons of chips every hour
With annual production of 9,000 metric tons of chips and snacks, Swiss company Zweifel Pomy-Chips AG recently achieved a turnover of over 300 million Swiss francs. Some 440 employees play their part in the success of the family-owned empire. They ensure the smooth production of around 50 different snack articles – and are also responsible for the engineering of production plants with capacities of up to 3,000 kilograms per hour.
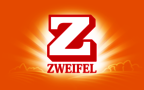
"Electrical diagrams are created with just a few clicks. And if a function changes, then all documents in which it appears immediately change too. If you need synergies, you need Engineering Base."
Lo Giudice, Project Manager at Zweifel Pomy-Chips AG
Learn more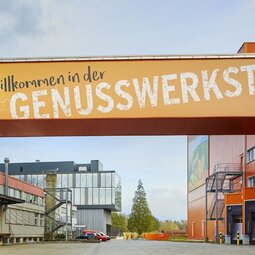
© Zweifel Chips & Snacks AG
Modular design with the Typical Manager
As they strive to increase efficiency, most successful plant manufacturers specialize in specific industries, niches and technologies where they can rely on their experience and proven solutions. This is an ideal scenario for implementing modular design – and for the Advanced Typical Manager in Engineering Base.
This allows planning to be carried out using pre-tested standard modules and greatly simplifies the work of development engineers in production plant construction. With the additional benefit of user-friendly option and variant management, the Typical Manager enables shorter project turnaround times and superior plant quality.
Changes in a typical only need to be entered once, as the ‘single source of truth’ principle means that up-to-date plant data is universally available at all times. In practice, this means fewer typicals, fewer errors and higher quality.
Planning in three dimensions is important for making optimum use of space. No matter whether it's a production hall, a conveyor system or a control cabinet, the physical path of piping, cable trays or wires needs to be precisely calculated and documented. The transfer to 3D systems is often carried out manually in practice. However, AUCOTEC and UNITEC have developed a platform that links planning in Engineering Base with all commonly used 3D models, regardless of the manufacturer and without any errors.
This provides bidirectional exchange between all systems and reduces the need for manual reworking. Components defined in Engineering Base are transferred to the 3D representation, while all 3D objects can continue to be used in Engineering Base. This complete data consistency massively increases the efficiency and quality of plant construction.
"On a data level, it makes little difference whether it's a process plant, a machine or a control cabinet when using a structured data model. That's why they can all be combined in a unique way to form an integrated project in Engineering Base – and can be mapped within it."
Dirk Grief, Application Consultant
