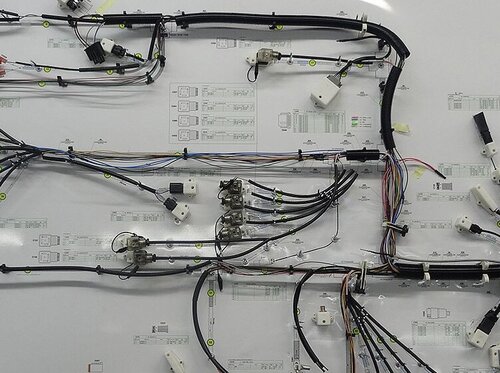
Wiring Harness Design and Manufacture
From modular design to modular manufacturing
Contact:
Engineering Base Cable is the ideal software for planning and specifying the electrical components, connectors and wiring in a vehicle. The installation space requirements for the harness are determined in parallel to this using, of course, a 3D mechanical design tool. The 3D wiring harness integration capability of Engineering Base means the experts from both disciplines receive all the information they need in their usual work environment – without having to concern themselves with more detailed aspects of their counterparts' work.
The object-oriented data model of Engineering Base Cable allows all disciplines to access all data and work on it simultaneously. This makes the software a single source of truth. From electrological definitions and the 2D topology to the 3D model – Engineering Base Cable provides an overview of the entire planning data at all times.
Engineering Base Cable is perfect both for determining the electrical components and connectors in a vehicle and for the 3D harness data. All data is then aggregated in Engineering Base. Once routing of the individual wires has been carried out, the 2D harness derivations and subsequent documentation will be generated automatically there.
The digital twin of all relevant electrical and mechanical data is reflected in the Engineering Base data model and enables extensive data analyses and the provision of data for subsequent processes. All components and their properties and interrelationships are available in the model and can be evaluated and detailed. For example, suitable contact parts are determined automatically. Follow-up documents and data for manufacturing processes are available.
Besides administering the data transfer, the plug-in for the integrated 3D tool also sets up live synchronization between the digital twin in Engineering Base and the 3D planning. This feature makes it easy to detect any modifications, such as new objects, deleted parts or adapted parameters. Synchronization at the click of a mouse puts 3D engineering and everyone else involved in complete control at all times.
The seamless integration of 2D and 3D in Engineering Base Cable enables a consistent form of harness development that speeds up processes considerably. Breaks in data and duplicate entries are a thing of the past, while harness and cable lengths can be defined faster and more accurately. This also has the effect of eliminating virtually all sources of error, improving quality and making the process as a whole far more efficient. As well as reducing prototype manufacturing costs, users also benefit from potential savings on expensive CAD licenses.
The benefits of cross-disciplinary work on the digital twin are particularly apparent here. Mechanical and electrical development engineers are able to work on the harness in parallel, thereby avoiding long waits for the other discipline's next planning step. All relevant information is instantly available. The mechanical side can therefore start to position connectors and determine the routing, while the electrical specialists continue to work on the circuit diagrams. The exact cable length is shown immediately once the electrics team has finalized the wiring.