The faster way to get H2-ready
The cooperation platform Engineering Base from AUCOTEC acts as a vehicle for reaching goals more quickly in all the aforementioned areas, despite their differing requirements. The company is therefore a highly sought-after partner for electrolyzer manufacturers who want to quickly produce more plants for more megawatts, for power distributors who need to convert and expand their gas networks and for operators whose plants need to be made H2-ready. Uniting them all is the huge pressure on their projects. How can Engineering Base help with this?
Consistent, agile engineering
The cornerstone as always is Engineering Base's centralized, cross-disciplinary data model for consistent, agile engineering. "The various sectors also benefit greatly from the fact that we also apply any findings from other industries in which Engineering Base is used successfully," explains Henry Bloch. AUCOTEC's modular design know-how is a powerful asset for electrolyzer development. And the teams planning and constructing the necessary hydrogen gas network benefit from Engineering Base's comprehensive process engineering functionalities and profound expertise, built on decades of international success in power distribution. "Process engineering is just as important as power distribution knowledge for the future H2 infrastructure," emphasizes Bloch.
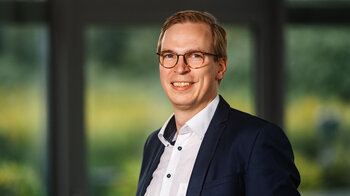
Modularization for much greater efficiency
In the electrolyzer sector, the first manufacturers are already benefiting from the cooperation platform's data-centric modularization. These companies need highly standardized modules that can be 'clicked together', because they scale up plants and output by numbering up the modules, rather than increasing the size of containers and machines. "Once the modules have been designed in Engineering Base, 90 percent of the work is done," says Meier. "Simply select the modules, assemble the project and connect it all up. Everything, along with the connections, fits seamlessly into the overall concept – even including the control system configuration. The accompanying documentation is largely produced automatically."
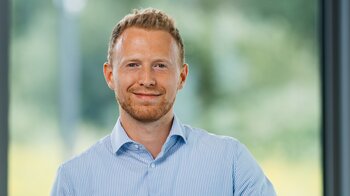
The digital twin makes things faster and more economical with zero errors
Operators planning to switch to H2 as an energy source for their plants in the future face a different set of challenges. The conversion work needed for this requires reliable as-built documentation, preferably in the form of a directly editable, cross-disciplinary plant model. This digital twin is contained in Engineering Base, having being either developed directly in the system or created by migrating legacy data, where the existing information is digitally processed and enhanced by means of an interface. The Engineering Base maintenance app also makes it easier to keep the twin up to date. "This means the confusing red markups and time-consuming searches that traditionally affect discipline-specific data silos are a thing of the past," says Bloch. In this way, Engineering Base can take electrolyzer manufacturers, network planners and plant operators from the slow lane to the fast lane – with zero emissions of course. And this enables the production and use of H2 to advance more quickly.